Engineering Solutions
At FEROSA QUALITY CONSULTANT, our Engineering Solutions focuses on offering you exceptional consulting services in engineering and quality management. Our expertise in process optimization ensures that your projects reach their highest potential in performance and efficiency.
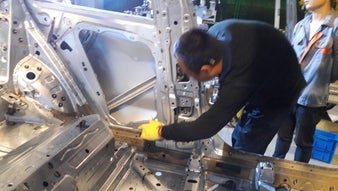
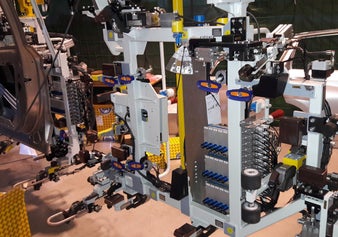
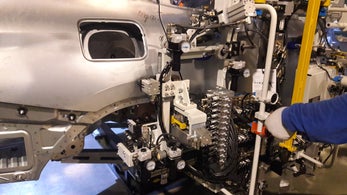
What we offer
Our engineering consulting services are designed to provide you with a thorough analysis and actionable solutions tailored to your specific needs. Whether you are working on a new project or looking to improve an existing system, our team of experienced consultants is here to support you. We specialize in a wide range of engineering disciplines including mechanical, electrical, and industrial engineering, ensuring that all aspects of your project are covered comprehensively. Our goal is to help you achieve excellence in design, implementation, and maintenance of your engineering projects.
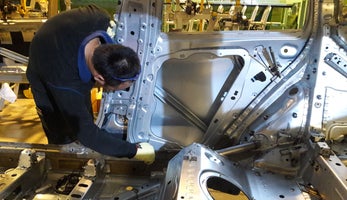
Comprehensive Engineering Consulting
Are you struggling to keep up with the ever-evolving quality standards and regulations in your industry? Ferosa Quality Consultant is here to help. Our team of seasoned engineering and quality management experts will work closely with your business to ensure you remain competitive and consistently meet the needs of your customers and international standards. With our proven track record of success, you can trust that your company is in capable hands. Don't let quality issues hold you back – partner with Ferosa Quality Consultant and take your business to new heights.
Quality-Based Engineering Services:
- Developing automated systems for manufacturing and assembly lines that increase efficiency and reduce human error.
- Creating apps that improve user engagement and productivity in various sectors, such as the Automotive and Healthcare industries.
Ferosa Quality Consultants, like many consulting firms, likely specializes in identifying, analyzing, and providing engineering solutions to address design errors in products and processes, as well as improving manufacturing practices. Below are some possible services and solutions they may offer based on your description:
Design Error Analysis
- Root Cause Analysis: Systematic investigation to identify the underlying causes of design errors, using techniques such as Failure Mode and Effects Analysis (FMEA) and Fishbone Diagrams.
- Design Reviews Engineering: Conduct thorough reviews of existing designs to ensure compliance with specifications, standards, and best practices.
- Computer-Aided Design (CAD) Validation Engineering: Using CAD tools to simulate design concepts and verify performance before production.
Prototype Development
- Rapid Prototyping: Producing prototypes quickly for testing and validation purposes, reducing time-to-market for new products.
- Testing and Validation: Performing rigorous testing on prototypes to identify any potential flaws in design or performance.
Manufacturing Solutions
- Process Improvement: Analyzing existing manufacturing processes to identify inefficiencies and areas for improvement, such as reducing waste or cycle time.
- Lean Manufacturing Techniques: Implementing Lean methodologies to optimize workflows, enhance productivity, and minimize waste.
- Quality Control and Assurance: Establishing quality control measures and systems to ensure products meet required standards and specifications.
Training and Development
- Workshops and Training Programs: Offering training sessions for teams on best practices related to design, manufacturing, quality assurance, and continuous improvement methodologies.
- Cross-functional collaboration: Encouraging collaboration between design and manufacturing teams to ensure alignment and comprehensibility of products.
Regulatory Compliance
- Compliance with Regulatory Standards: Assisting companies in understanding and focussing on customer-specific requirements and meeting industry-specific regulatory requirements, such as in Automotive: IATF-16949/TS also for Medical Device regulations such as ISO 9001:2015, ISO 13485:2016, GMP/GDP, FDA 21 CFR 11, EUMDR, ANSI, or compliance to Environmental Health and Safety Standard like ISO 14001:2015 and QHSE. We can also bring your organization's Artificial Intelligence Quality Management System (AIMS) up to speed in compliance with ISO/IEC 42001: 2023. which as a result of the introduction of AI significant contribution to economic efficiency and acts as a formidable assistant in the reduction of material waste and production cost, which also drives cost-effectiveness by enhancing precision in engineering.
- Documentation and Reporting: Helping clients prepare the necessary documentation for compliance audits and product certifications.
Continuous Improvement Initiatives
- Feedback Mechanisms: Implementing, see our CAPA risk-based approach.
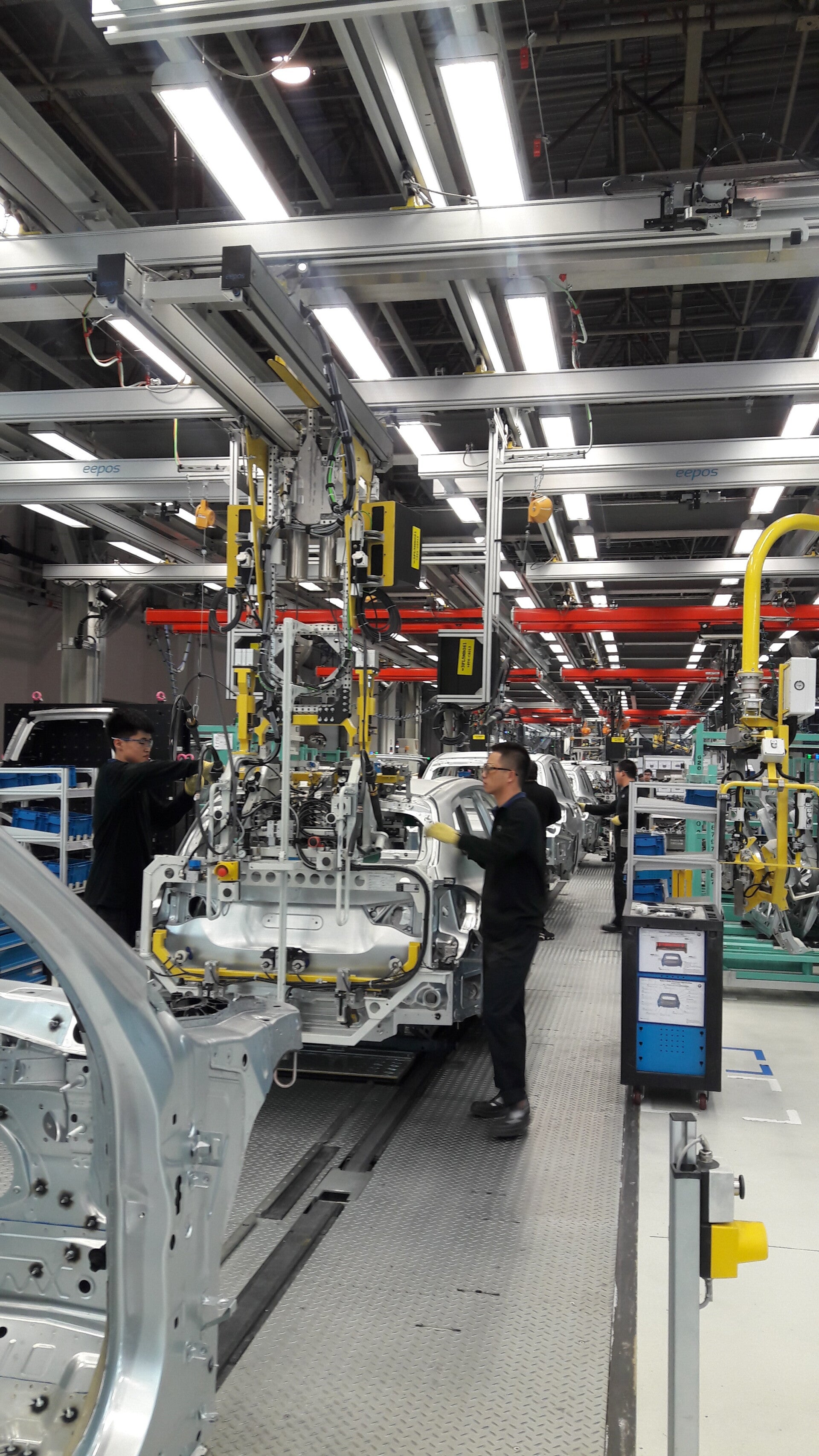
Customer Complaint and CAPA Approach:
A Customer Complaint and Corrective and Preventive Action (CAPA) mechanism is a systematic approach designed to handle customer complaints effectively while ensuring that issues are resolved and prevented from reoccurring. Here’s our structured process for implementing this mechanism:
Complaint Receipt and Acknowledgment
- Channels for Complaints: Establish multiple channels for customers to submit complaints (e.g., phone, email, website, social media, or the organization’s Sales Force Cloud platform).
- Acknowledgment: Respond to the customer promptly, acknowledging receipt of the complaint. Provide an estimated timeline for resolution.
Complaint Logging and Documentation
- Record Keeping: Maintain a centralized complaint log that includes details such as the customer's information, complaint description, date received, and initial response.
- Category Classification: Classify complaints based on type (e.g., product quality, service issues, delivery problems) for better analysis.
Investigation and Root Cause Analysis
- Preliminary Assessment: Quickly assess the severity and urgency of the complaint.
- Data Gathering: Collect all relevant information regarding the complaint, including product details, service records, and customer history.
- Root Cause Analysis: Utilize techniques such as the 5 Whys, Fishbone diagram, or Fault Tree Analysis to identify the underlying causes of the complaint.
Corrective Action Implementation
- Action Plan Development: Develop a clear action plan to address the identified root causes. This may include changes to processes, training, or product modifications.
- Execution: Implement the corrective actions promptly and monitor their effectiveness.
- Customer Communication: Inform the customer of the corrective actions taken and provide updates on the resolution progress.
Preventive Action Development
- System Review: Review processes and systems to ensure that similar complaints are not likely to occur in the future.
- Process Improvement: Implement changes to procedures, quality control measures, training programs, or supplier relationships based on insights gained from the complaint.
- Training and Awareness: Ensure that employees are aware of the changes and are trained to prevent similar issues.
Effectiveness Check
- Follow-Up: After implementing corrective and preventive actions, follow up with the customer to ensure their satisfaction and the effectiveness of the solution.
- Monitor Trends: Analyze complaint data over time to identify trends and further areas for improvement.
Documentation and Review
- Record Outcomes: Document the entire process, including actions taken, results, and follow-up communications.
- Management Review: Regularly review complaint resolution outcomes and the effectiveness of the CAPA process at management meetings to ensure ongoing improvement.
Continuous Improvement
- Feedback Loop: Establish a mechanism for learning from each complaint. Use insights to improve products and services continuously.
- Stakeholder Engagement: Involve relevant stakeholders, including employees and customers, in the review process to gather diverse perspectives on improvement opportunities.
.
Process Optimization
Efficiency is key to the success of any engineering project. Our process optimization services focus on identifying and eliminating inefficiencies within your current systems. We employ state-of-the-art tools and methodologies to analyze your workflows, identify bottlenecks, and recommend improvements. From supply chain management to production processes, our goal is to maximize your operational efficiency and reduce costs. By optimizing your processes, you can increase productivity, enhance product quality, and accelerate time-to-market.
Staying competitive in today's global market requires a relentless focus on quality and operational excellence. At Ferosa Quality Consultant, our team of seasoned engineering and quality management experts is here to help your business thrive. We'll work closely with you to ensure your operations are optimized, and your products and services meet the rigorous demands of customers and international standards. With our proven track record and industry-leading expertise, you can trust Ferosa Quality Consultant to be your strategic partner in driving sustainable growth and success. Invest in quality, invest in Ferosa.
Conclusion
A well-structured Engineering Solution with well-planned Process Optimization combined with a well-documented Customer Complaint and CAPA Approach mechanism in place, not only resolves issues but also fosters trust with customers, enhances product and service quality, and drives continuous improvement. By dedicating time and resources to understanding customer feedback, organizations can build stronger relationships and improve their offerings.
Contact Ferosa Quality Consultant for the implementation of CAPA in your organization
Get in Touch
Ready to elevate your business with expert consulting in engineering and quality management and Regulatory Compliance?
Contact us today to discuss how we can help!
Contact FEROSA QUALITY CONSULTANT to learn how we can help.
Contact information
FEROSA QUALITY CONSULTANT
Email: ferosa@consultant.com
Tel: +31 62 5484 224
KVK-number: 94564353
Btw-id:NL005094977B90
Create Your Own Website With Webador